We conserve resources with recycled concrete
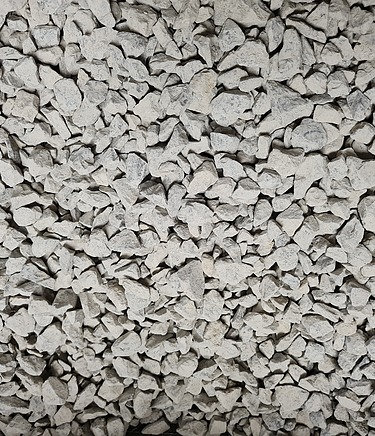
We are committed to using resource-saving building materials for the realisation of sustainable construction projects
For the STRABAG Group and its German subsidiary ZÜBLIN, recycled concrete (R-concrete) is an important building block for the sustainable realisation of construction projects. Given the increasing scarcity of primary raw materials, the systematic recycling and reuse of construction waste is a key factor to achieving our goal of becoming climate neutral along the construction value chain by 2040.
Recycled concrete (also known as resource-saving concrete) is produced with a significant proportion of recycled concrete aggregate. The production of recycled, resource-saving concrete involves the use of recycled construction aggregates, for example from concrete waste and building rubble, instead of standard raw materials such as gravel, sand and crushed rock. Recycled concrete contributes to systematically reducing the consumption of previously heavily exploited primary resources. The use of recycled concrete in building construction is also a decisive step towards circular design and construction – ideally with closed material cycles.
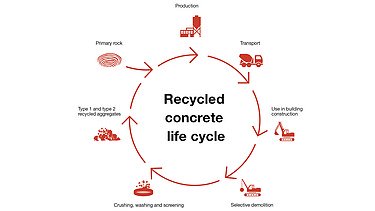
Short transport distances for increased environmental quality
The distance travelled is a key factor in the carbon footprint of R-concrete. Shortening the distances between demolition, processing and reinstallation reduces carbon emissions and makes the use of recycled concrete more sustainable. Short transport distances are therefore essential for the environmental quality of resource-saving concrete. The appropriate infrastructure exists primarily in large urban areas. One example is the Circular Construction & Technology Center (C3) in the former oil port of Bremen, where STRABAG Environmental Technology plans to process and produce recycled concrete for the greater Bremen region. More of these circular economy centres are planned at other STRABAG locations in the future.
Use in building construction also possible for load-bearing structures
Recycled concrete offers considerable potential in building construction, where it can also be used for load-bearing components. Overall, recycled concrete aggregate is quite suitable for the production of most of the standard concrete types used in Germany. Their specific properties can be accounted for in the production process through technological adaptations. As a result, there are no restrictions with regard to exposed concrete qualities or the installation and processing of recycled concrete on the construction site.
The recycled aggregate should contain as high a proportion of crushed concrete as possible in order to ensure a sufficiently high compressive strength of the recycled concrete. There are different national specifications in this regard. In Germany, for example, two different types of recycled concrete aggregate are commonly used: crushed concrete aggregate (type 1) must consist of at least 90 % pure concrete rubble and may contain no more than 10 % from bricks or calcareous sandstone. In the case of building rubble aggregate (type 2), on the other hand, the masonry content may be up to 30 %.
Construction waste: recycling vs. downcycling
A large part of mineral construction waste is already recycled for a variety of purposes, albeit predominantly at a lower quality level, in road construction, e.g. in unbound frost protection layers and base courses (downcycling). The circular use as an aggregate for recycled concrete in building construction (recycling) is still an exception in some countries, including Germany. However, the increasing number of pilot projects with recycled concrete that ZÜBLIN has recently implemented with various clients (e.g. Mercedes-Benz Factory 56 in Sindelfingen and Stadtquartier Henriettengarten in Kirchheim unter Teck) or is currently in the process of realising (e.g. Esslingen District Office) indicates a reversal of the trend.
Based on its experience, the STRABAG Group advises its clients about the options for the increased use of recycled concrete on a selective and needs-oriented basis in order to promote the transition towards a sustainable and circular construction economy.
One example involves the secondary school in Cologne Deutz and the neighbouring sports and office complex, where STRABAG is building new classrooms and sports facilities for 1,000 students as well as office space on a gross floor area of over 40,000 m². The project will utilise 18,000 m³ of recycled concrete. Of this amount, we are recycling around 9,000 tonnes of concrete rubble ourselves for a recycling rate of around 45%. Looks are also important in this project. On almost three quarters of the interior walls, the concrete will remain visible (exposed concrete class 3). This places higher demands on the surface colour, which we meet through the addition of aggregates. It’s a project to be proud of – both visually and in terms of sustainability and resource conservation.
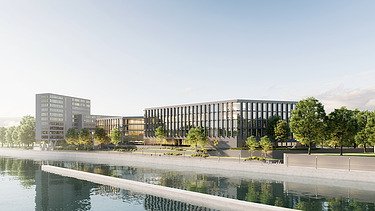
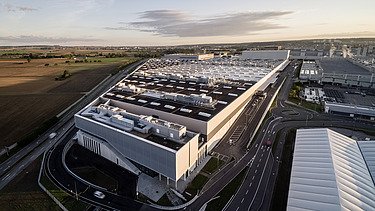
Factsheet:

Recycling concrete