Circular Construction
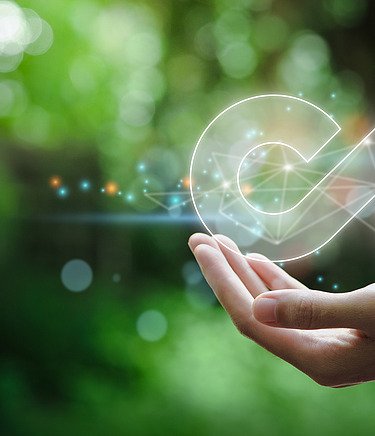
Our work on circular construction
The UN International Resource Panel’s Report on Assessing Global Resource Use cited an annual global resource consumption of almost 90 billion tonnes back in 2017 – an amount that could double by 2050. That is significantly more than can be renewed every year, putting us a long way from a sustainable way of life. Some 70% of global greenhouse gas emissions can be traced back to the production and consumption of raw materials. The construction industry plays a significant role in this context – a fact that we are well aware of.
More than half of the total waste generated in Germany and Austria results from construction and demolition waste. This makes it difficult to talk about sustainable construction without using the terms circularity or circular economy. We must take a holistic view of construction projects, manage building materials in a way that conserves resources, and rethink the entire industry. At STRABAG, we are committed to the responsible use of building materials throughout their entire life cycle – from the extraction of raw materials and their use in construction to dismantling and recycling. This whole set of actions is referred to as the value stream.
The four principles of circular construction
One thing is clear: the linear economy (take – make – dispose) has no future in a world with finite resources. It must give way to a holistic circular economy. At STRABAG, we consider the entire life cycle of a building and take dismantling, disposal and recycling into account right from the planning stage. We create material cycles and extend them by returning used materials into that cycle. This enables us to reduce waste and conserve resources. In this way, we can gradually achieve a circular construction process.
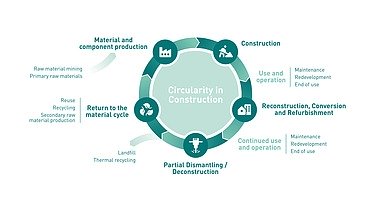
1. Increase product and material efficiency
Improved design, resource-saving construction methods and the use of sustainable building materials significantly optimise the material efficiency and environmental footprint of buildings. Hybrid construction methods using steel, lightweight materials or wood, for example, make it possible to significantly reduce the amount of concrete required. Modular construction, with the highest possible degree of prefabrication, also ensures less waste in the production process, shorter construction times and simplified demolition.
Using optimised construction scheduling with LEAN.Construction methods and specific analysis tools, we continuously examine how construction site logistics can be made more efficient and how resources can be used as economically as possible.
Find out more about conserving resources with LEAN.Construction
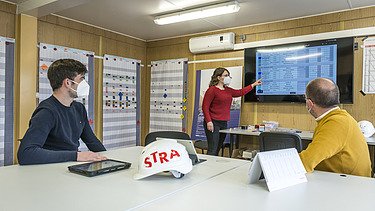
2. Extend the use of our products
Using buildings for as long as possible, refurbishing, modernising or renovating them instead of razing them to the ground – this is the resource-saving alternative to the construction of entirely new buildings. Through thermal refurbishment and the optimisation of energy concepts, existing buildings can be operated in a more energy-efficient manner. Refurbishment also uses less “grey energy” than the construction of new buildings. Grey energy refers to the total amount of “invisible” energy used during the entire life cycle of a product, from the extraction of the raw materials to production and disposal.
3. Establish material cycles
Instead of simply throwing materials away after use, the aim of establishing material cycles is to recycle and process them in such a way that they can be returned to the construction cycle. In Germany alone, we operate 82 recycling and recovery sites to help us do just that.
Recycling means keeping the materials in the cycle in as consistent a quality as possible. We are already achieving this in our asphalt recycling, using recycled asphalt wherever possible or permitted. Our state-of-the-art asphalt mixing plants, such as the one in Hausleiten, Austria, can in theory produce asphalt with a 100% recycled content.
Downcycling, on the other hand, means that materials of lower quality are reused, for example when demolished concrete is used in the base course during road construction. To avoid downcycling reusable materials, it is already possible to reprocess asphalt and concrete from demolition waste into new, high-quality recycled building materials. This systematically reduces the need for primary raw materials and helps to conserve our finite resources. When realising new construction projects, the aim must be to use secondary raw materials as much as possible.
For the widening of the A8 Enztal crossing near Pforzheim in Germany to six lanes, we are removing a total of around 1.2 million cubic metres of earth on behalf of the client, Autobahn GmbH des Bundes, processing it on site and reusing almost all of it. Around one third of the excavated material – including shell limestone, concrete and old asphalt – is reprocessed Into a high-quality mineral substitute material that benefits the other STRABAG construction projects in the vicinity as well. The clay contained in the soil also serves as a natural sealing material. All in all, a resource-conserving approach that also saves money.
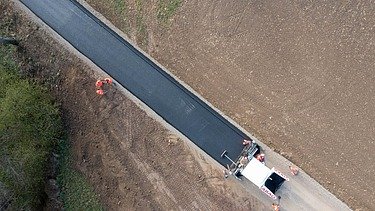
Urban Mining
An important component of circular construction is a process known as urban mining. This means viewing densely populated areas – especially large cities – as enormous raw materials repositories and using them for the circular economy. Long-lived goods in particular, such as concrete or asphalt, should not simply be demolished and hauled off for disposal at great expense, but are recycled on site and reused in the region. This enables the raw materials contained within our roads, buildings and soils to be reused as secondary construction products in a resource-saving and climate-friendly way.
We also want to bring business and research together in our recycling competence centres. STRABAG Environmental Technology is currently realising a state-of-the-art technology and recycling centre for urban mining and construction waste processing, C3 Circular Construction & Technology Center, on the 13-hectare site of a former oil port in Bremen. In the future, we will be working and researching here in collaboration with universities and start-ups in order to advance construction waste recycling and optimise our processes and products.
Find out more about the C3 Circular Construction & Technology Center Bremen
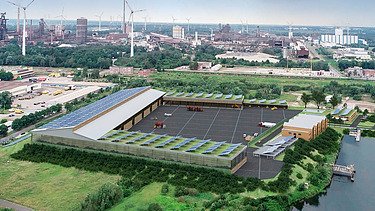
4. Build with an eye on recycling and reusing materials
Taking demolition and dismantling into consideration already during the design phase facilitates the reuse of a building’s or other structure’s parts even after the end of its service life. In addition to recyclable materials, precast concrete parts are also suitable for this purpose. Staircases and elevator shafts are usually produced in one piece, are very durable and have standardised dimensions, so they can be removed after initial use and reused without great effort.
Find out how STRABAG is cutting carbon emissions through modular construction
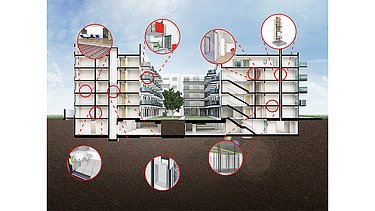
Of course, not all materials can be recycled. For these material groups, we look for alternatives that can be replaced by recycled or renewable raw materials. We are constantly researching and testing new materials and construction methods to achieve this goal.
Find out more about sustainable building materials
In the future, it will be possible to produce cement without using environmentally harmful clinker as a binding agent by using waste products instead. A lot is also happening in the field of concrete. Carbon or glass fibre mesh is being used to reinforce concrete, for example, in order to reduce the amount of steel needed. STRABAG has also collaborated on individual projects with our internal project developer
STRABAG Real Estate to test insulating materials made of sheep’s wool.