LEAN Construction: the lean way to build
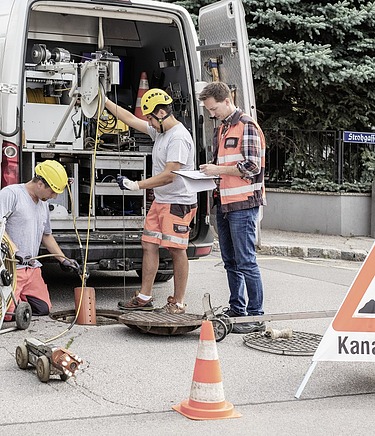
We use the LEAN Construction way of thinking and working in all our projects. This not only saves us time and money but also makes our work more sustainable. Because you don’t reduce emissions only with new materials or particularly innovative inventions; avoiding waste is another powerful lever for change.
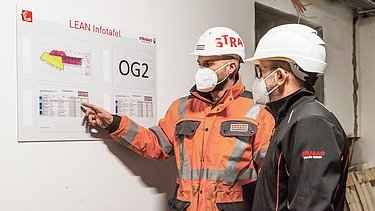
The aim of LEAN Construction is to design processes and workflows to be as efficient, as precise and as lean as possible. In LEAN Construction, people, machines and methods work together optimally to avoid disruptions and waste in the process flow.
This enables us not only to optimise time and cost structures and to closely coordinate the individual work steps, but also to reduce the unnecessary consumption of resources – without compromising on quality. That is both economical and environmental!
Four LEAN principles for sustainable construction projects
Even before construction begins, we use LEAN Construction to set the course for a successful, sustainable building project. We do so by taking an end-to-end view of our construction projects – from planning and design to the actual construction – and arrange the work processes according to the four LEAN principles:
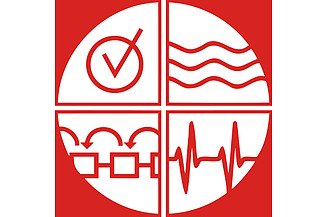
Flow: Continuous flow of all necessary resources and information.
Tact: Identifies repetitive work steps and optimally coordinates them with each other.
Pull: Machines, materials, information and people are assigned to the process as needed.
Zero defects: Mistakes can happen, but they should be discussed and analysed in the team afterwards in order to avoid deficiencies, rectifications and problems in the future.
Lean processes in the design-and-build process
STRABAG plans precisely which resources, equipment or work steps are needed when, where and to what extent. We also examine how a construction site can be designed and managed more efficiently. On this basis, we take appropriate efficiency measures and use LEAN systems for construction process management, for example, to prevent identified waste and to optimally synchronise trades in order to avoid downtimes. This also applies to the use of equipment and construction machinery by reducing unnecessary idle time.
Better integrated, better for the environment!
Our logistics partners are always included in this process. When production facilities and suppliers are properly integrated into the construction site, this not only reduces waiting times and storage space, but also avoids unnecessary heavy traffic and so greatly reduces emissions. With precise planning and timing, we also keep mixing plants running so they don’t have to be constantly restarted when needed. This is often the case with logistics that are not optimally coordinated, resulting in enormous additional energy consumption. At our Kennedy Garden residential project in Vienna, the suppliers and subcontractors were able to announce deliveries using an app in order to best plan their arrival through the narrow access roads depending on the current traffic situation. This helped reduce idles times to zero.
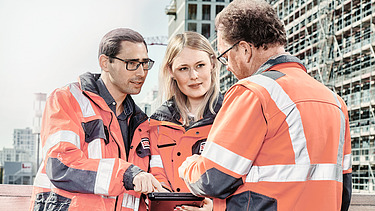
LEAN also greatly benefits the logistics on the construction site itself. The construction planners, for example, can make sure that materials, equipment and people are always in the right place at the right time. Aspects that may seem insignificant at first glance also play a role. The proper placement of materials on the construction site, for example, significantly reduces how much the crane operator needs to move his crane, which can greatly reduce emission levels when calculated across all of STRABAG’s large construction sites.
Learning together through LEAN Construction
With LEAN Construction, we think through our processes and process steps systematically. The knowledge that is gained and the improvements that are achieved are not limited to a single project. They are transferable, scalable – and in the best sense of the word: sustainable.
Factsheet:

The lean way to build