Mischek Prefabrication: all systems go for the reduction of greenhouse gas emissions
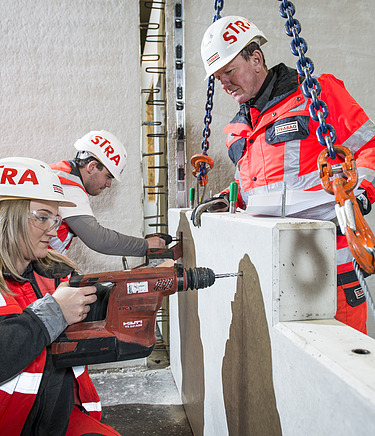
Reducing CO2 through prefabrication
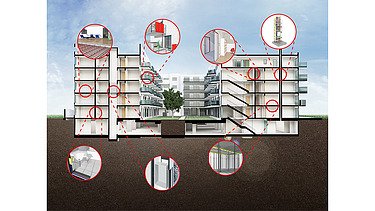
Innovative industrial prefabrication is an important factor for mastering the pressing challenges of urbanisation and the need for affordable housing. Prefabrication systematically reduces noise, dirt and the need for road closures during the construction phase. The higher the percentage of Mischek’s modular products used in construction, the less manual work is necessary on the construction site itself.
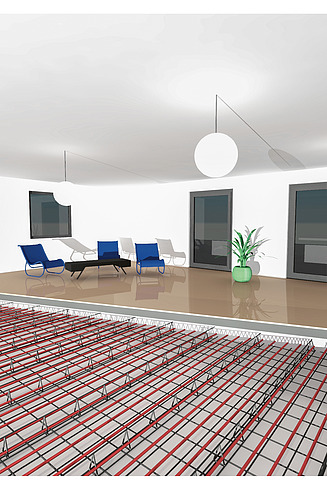
The advantages of prefabrication
Our building components aren’t just prefabricated robotically at our plant but are also fitted with the sanitary and electrical installations before being delivered to the construction site. This allows us to reduce the storage space required on site and to carry out up to 50 % of the work beforehand. Walls, ceilings, lift shafts and balconies/terraces are manufactured in advance in a controlled production facility, which guarantees the best quality of the reinforced concrete design.

Our products help to address the current challenges and allow us, as a pioneer in our industry, to develop and produce intelligent and innovative prefabricated reinforced concrete elements. The more tasks we can shift from the construction site to the factory, the better.
Systematically reducing carbon emissions
We are already converting the entire Mischek plant to a green energy supply, which is produced directly on the factory premises. A photovoltaic system on the roof of the production halls already provides renewable electricity. In addition, a biomass boiler provides environmentally friendly heat. This means that Mischek is well on the way to producing the finished parts in a completely climate-neutral way.
Modular system vs. in-situ concrete construction
Prefabrication helps to cut our greenhouse gas emissions. A crucial factor here is to reduce the number of material transports to the construction site. Using the products from Mischek cuts site deliveries of building materials by up to 40 %. For a residential building comprising 100 flats with an average of 65 m² of living space each, the modular system saves around 65,000 kg of CO2 equivalent compared to conventional in-situ concrete construction. That corresponds to the emissions from almost 21,000 litres of diesel fuel.
*All values are based on a comparison of in-situ concrete construction versus the modular Mischek system
Robots at the factory
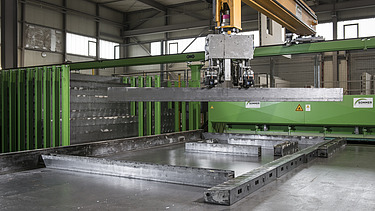
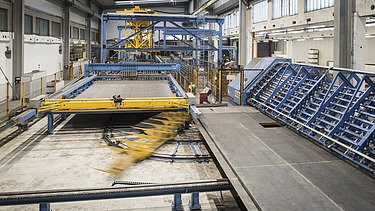
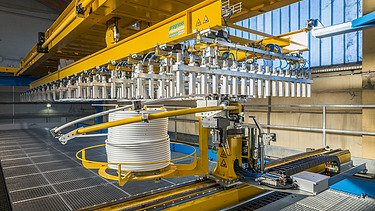
Factsheet:

Reducing CO2 through prefabrication