Eigenrieden Quarry: Climate neutrality in the extraction of raw materials
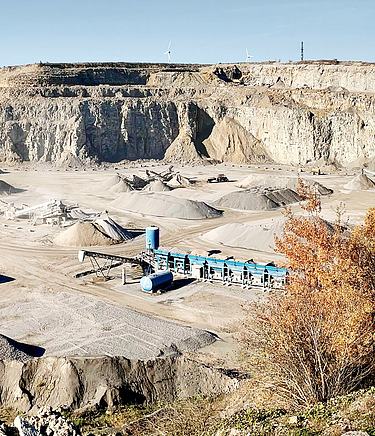
STRABAG pilot project of Mineral Baustoff GmbH for decarbonisation in Thuringia
The Eigenrieden limestone quarry aims to gradually reduce CO2 emissions associated with the extraction of raw materials and the production of building material aggregates and crushed stone, with the goal of becoming the first climate-neutral quarry in Germany by the end of the current decade. This decarbonisation pilot project makes the facility, operated by our subsidiary Mineral Baustoff GmbH in Thuringia, a pioneer in sustainability, environmental protection and innovation throughout the industry. The project is also intended to set an example and serve as a model for the climate-friendly transformation of other raw material sites within the STRABAG Group.
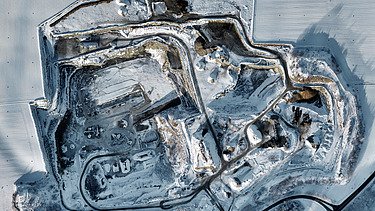
The Eigenrieden limestone quarry currently has a deposit of about 6 million tonnes of rock in the Lower Muschelkalk strata. Mineral Baustoff GmbH produces roughly 220,000 tonnes of building material aggregates and crushed stone here every year. To date, the equipment and machinery at the quarry have been powered conventionally using diesel fuel. As a result, the facility emits about 490 tonnes of CO2 a year. The aim is to gradually reduce these carbon emissions to almost zero until 2030 through a series of steps involving several subprojects. To achieve its decarbonisation goals, Mineral Baustoff GmbH is switching from diesel-powered equipment to electricity or electric powertrains and climate-neutral fuels – step by step and across all three stages of the production process: extraction, processing and loading.
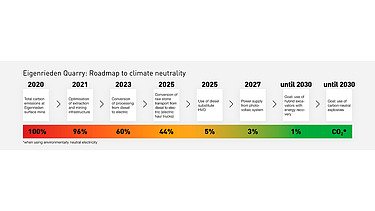
New processing plant: PV panels for sustainable solar power
At the end of 2023, a high-efficiency, electric-powered stationary processing plant has replaced the previously used diesel-powered mobile equipment. The new crushing and screening plant that is already under construction will – like all STRABAG locations and construction sites in Germany – be powered by green electricity from hydropower sources. A high-performance dust mitigation system and noise-absorbing insulation of the crushers, screening machines and belts help to minimise dust and noise emissions.
By 2027 at the latest, the energy needs of the raw material processing plant are to be largely covered by solar power from an in-house photovoltaic system. To ensure the autonomous operation of the plant, Mineral Baustoff GmbH plans to have two PV arrays with electricity storage built on land adjacent to the quarry.
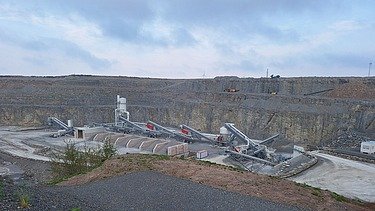
Electric autonomous haul trucks for transport in the quarry
To systematically reduce carbon emissions during raw material extraction at Eigenrieden, we are primarily focusing on the gradual introduction of electric-powered, autonomously operated haul trucks.
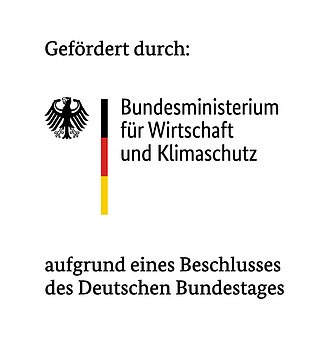
Mineral Baustoff GmbH is one of seven partners in the ongoing ELMAR research project (8/2022–7/2025), which aims to integrate electric heavy-duty machines into the decarbonisation of the raw materials industry. The project, led by RWTH Aachen University, has received €6 million in funding from the German Federal Ministry for Economic Affairs and Climate Protection (BMKW). Vehicle manufacturing partner in the project is Volvo.
After initial test runs in the fall of 2024, the start of trial operations of the electric and self-driving Volvo heavy-duty dump trucks in Eigenrieden is planned for the spring of 2025. The aim is to use three of these zero-emission tipper trucks in the quarry in the future to transport the extracted limestone to the processing plant. The prerequisite for this is that the tipper truck prototype from the research project proves itself as a market-ready product. These trucks will not only reduce the carbon footprint of the quarry; they will also make a lasting contribution to improving occupational safety and health during the raw material extraction work.
HVO biodiesel and hybrid powertrains
Starting in 2025, the excavator used in the extraction process and the large loaders for loading the trucks will be fuelled with synthetic biodiesel (HVO diesel from hydrogenated vegetable oil) instead of conventional diesel fuel. The use of biofuel will not only reduce carbon emissions by more than 80%; it will also significantly lower particulate matter pollution and nitrogen oxide emissions. As soon as appropriately sized extraction machines are available on the market, the conventional excavator will also be replaced by a modern, fuel-saving hybrid model with energy recovery to further improve the carbon footprint of the quarry operations.
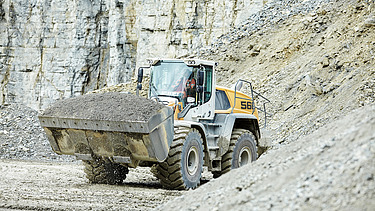
Factsheet

Quarry Eigenrieden