Alternative drive technology for construction machinery
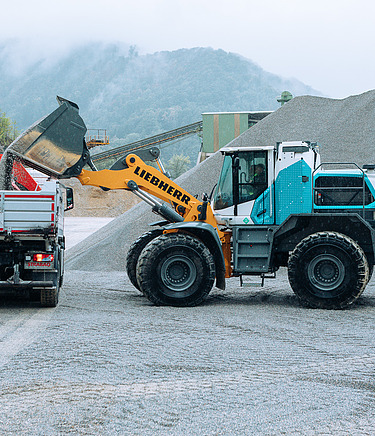
Why we need environmentally friendly fuels
The construction industry is still lacking comprehensive solutions as to how alternative drive technology can be used on construction sites. This is why STRABAG is testing promising potential: instead of diesel and gasoline, we want to rely on hydrogenated vegetable oils (HVO), electromobility and hydrogen propulsion in the future.
Why do we need alternative engine technology?
Fuels are the largest CO2 emitter at STRABAG – 40 percent of emissions are caused by the use of diesel alone. Our construction machinery requires a large proportion of this. Alternative drive technologies are therefore an important element in reducing emissions. If we switch our construction machinery to environmentally friendly fuels, we can make a big step towards achieving climate neutrality by 2040. To achieve this, we need strong partnerships, especially in this sector, because only joint expertise can lead to long-term solutions.
What fuels are available for construction machinery?
We are testing various technologies and fuels in our offices and on our construction sites. Our car pool is already partly powered by electricity, with a growing number of electric devices. In construction operations, we see potential in hydrogen drives, which are significantly more sustainable compared to fossil fuels – both as a fuel cell drive and as a hydrogen combustion engine. HVO offers great potential as a climate-friendly diesel substitute, which is now permitted at normal filling stations.
A selection of our current projects in the field of alternative drive technology:
-
Hydrogen power
STRABAG and its partners Liebherr and Energie Steiermark have launched a pilot project for the use of a hydrogen-powered wheel loader in the Gratkorn pulpit quarry. The wheel loader was demonstrated in operation here for the first time. The hydrogen-powered wheel loader was developed by Liebherr. Instead of conventional diesel, the machine fills up with green hydrogen – the only waste product is water vapor. A hydrogen filling station for operating the wheel loader is currently in the approval process. Following on from this, we will test the device in daily use in the quarry for two years.
The hydrogen for the wheel loader comes from Energie Steiermark. This is the first time that green hydrogen will replace conventional diesel in the operation of large wheel loaders. This can save up to 37,500 litres of diesel or around 100 tons of CO2 per year.
-
Fuel cell
STRABAG is testing a slightly smaller fuel cell wheel loader from Liebherr. The wheel loader is being used as a demo machine in a basic hydrogen study supported by the Austrian Climate and Energy Fund, which is intended to provide experience for future developments.
The drive of the fuel cell wheel loader consists of several components. The pressure tank is filled with hydrogen and then, in the fuel cell, converted into electrical energy. A battery serves as a buffer for the energy generated. Finally, two electric motors drive the wheel loader – one for the drive, the other for the hydraulics. As a result, the machine runs electrically and with a high level of operational efficiency. This is the ratio of energy used to usable energy. Overall, the wheel loader has saved around 750 kilograms of CO2 during its operation compared to a diesel-powered machine.
-
Hydrogenated Vegetable Oils (HVO)
Hydrogenated Vegetable Oils (HVO) is a fuel similar to diesel that is produced without fossil resources. HVO is made from animal or vegetable residues or from tall oil, a waste product from cellulose production. The major advantage of this renewable fuel is that it can be added to a normal diesel tank without any conversion and is therefore suitable for a wide range of vehicles. Depending on the type of waste material used, up to 90 percent of CO2 emissions can be saved in comparison to fossil diesel.
Since the beginning of 2024, STRABAG has been testing HVO together with the fuel supplier Hoyer on various construction sites and construction material operations in road construction in Germany. A total of one million liters of diesel will be substituted. The HVO being used is strictly certified as sustainable. -
Electromobility
STRABAG is already working with various electrically powered construction machines. It is clear to us that the performance of the equipment is in no way inferior to that of a diesel vehicle. For smaller excavators or hand-operated equipment such as rammers or vibratory plates, the electric drive is already very useful. An electrically powered e-excavator from STRABAG was charged directly on site with green electricity during the construction of a wind farm in Trumau, for example. For large construction machines, however, an electric drive is still a special feature. That is why we are testing various e-vehicles from different manufacturers in everyday construction site operations: our quarry in Eigenrieden is set to become the first climate-neutral quarry in Germany. This also requires the construction machinery to be converted to alternative drive technologies. Electric skips will soon be used here in a pilot project.
STRABAG is already working with various electrically powered construction machines. It is clear to us that the performance of the equipment is in no way inferior to a diesel vehicle. For smaller excavators or hand-operated equipment such as rammers or vibratory plates, the electric drive can already be put to good use. For example, an electrically powered electric excavator from STRABAG was charged directly on site with green electricity during the construction of a wind farm in Trumau.However, an electric drive is still a special form of drive for large construction machines. That is why we are testing various electric vehicles from different brands in everyday construction site operations: our quarry in Eigenrieden is set to become the first climate-neutral quarry in Germany. This also requires the construction machinery to be converted to alternative drive technologies. In a pilot project, electric skips will soon be used here.
For STRABAG, reducing the energy consumption of construction machinery is an important building block in reducing emissions from construction sites on the road to climate neutrality by 2040. Tests like these under real conditions are needed to evaluate different technologies and their potential.