We recycle empty bottles. Why not our streets as well?
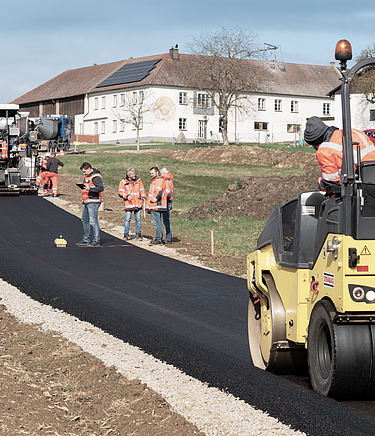
Spoiler alert: We’re doing that already! Because sometimes the pavement has deteriorated to such an extent that it is no longer enough to simply fill in the potholes – the entire asphalt has to be removed and replaced. When the old, removed asphalt is reprocessed for reuse, we speak of asphalt recycling. What few people know is that asphalt recycling has been common practice for years.
How does asphalt recycling work?
The process of recycling asphalt can be compared to the recycling of plastic bottles or used glass.
Asphalt recycling involves the removal of brittle or cracked asphalt by breaking away entire slabs or milling it off in layers using an asphalt milling machine. The stripped material is then taken to an official asphalt collection point, i.e. a landfill for used asphalt. There, the material is processed for reuse in our asphalt mixing plants, many of which, such as the one in Hausleiten, Austria, are state-of-the-art.
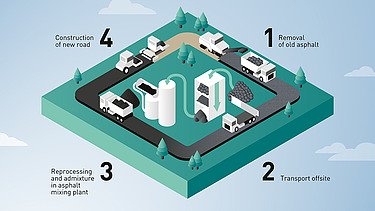
The asphalt is granulated, screened and separated in such a way that it can be used specifically for the various asphalt layers. After carefully checking the granulate, we mix it into the new material either cold or warm. New stone, granulate and bitumen are precisely dosed and processed into the reclaimed asphalt in the mixer.
With warm addition, the granulated asphalt is preheated in a parallel drum, which technically enables a recycling rate of 100%. The cold addition process allows for a recycling rate between 20% and 30%.
The recycled asphalt is then transported to our storage silos and from there to the construction site, where it is laid. Often, it is also possible to process the material directly on site using various methods, such as cold recycling. This not only reduces the transport distances but also uses less material.
A wonderful side effect:
Asphalt production uses bitumen as a binder to glue together the asphalt aggregates. Bitumen is a petroleum product obtained from the distillation of crude oil, a raw material whose use, for environmental reasons, should be avoided. The old asphalt already contains bitumen, so recycling asphalt not only cuts down on the need for new asphalt material, it also reduces the dependency on fossil petroleum. Recycling asphalt therefore has a twofold benefit, saving resources and protecting the environment.
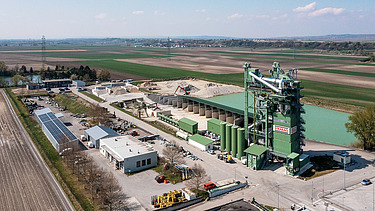
How much recycled asphalt does STRABAG use in its road construction projects?
STRABAG produces around 16 million tonnes of asphalt every year. We use asphalt recycling wherever possible, for example in our core markets. In Germany, reclaimed asphalt recently accounted for around 35% of total production, with 15% in Austria and 6% in Poland. For every tonne of asphalt that we reuse, we save just as much new asphalt.
We’re convinced that we can do even better! The industry is currently falling far short of its potential and often engages in downcycling. Due to the existing regulations, asphalt from the surface layer is often reused in deeper layers despite the fact that its quality is actually too high for this purpose. This doesn’t have to be the case.
STRABAG is constantly pushing the limits of what is technically possible in asphalt recycling, for example by conducting research into how to best achieve high recycling rates while maintaining high standards of product quality. Based on our findings over the past few years, we are certain that recycling rates can be significantly improved. In Germany in particular, the different standards in each of the different German states make a uniform approach difficult.
We’re currently in talks with our clients to convince them to use more recycled asphalt than previously stipulated in project tenders. Baden-Württemberg shows how higher recycling rates can be established in practice with its focus on maximum recycling. Hamburg, Schleswig-Holstein and Saxony-Anhalt also allow a higher proportion of reclaimed material.
We believe in the technology of asphalt recycling. And we are already successfully implementing them where our clients and partners are taking responsibility together with us. For example, on the Westautobahn A 1 in Austria, where we have increased the proportion of recycled asphalt to 40%.
Division manager Reinhard Kerschner even paved his private driveway using a maximum recycled content (70%). In our interview, he explains how it was done.
Factsheet:

Asphalt recycling